The bottomless drain
Can industrialized countries conserve their way out of an energy crisis?
We are not using most environmentally friendly energy source,” says Tor Helge Dokka.
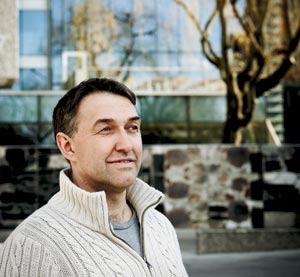
FROM 300 TO 80 KWH A YEAR
SINTEF researcher Tor Helge Dokka stands outside the 42-year-old Skedsmo apartment blocks, which are now being converted into low-energy housing. Before the craftsmen came, the apartments consumed approximately 300 kilowatt hours per square metre per year. When they leave, the number will have shrunk to 80.
Photo: Svein Tønseth
Neither wind turbines nor monster towers disturb the view where our taxi has stopped. Dokka, a veteran researcher from SINTEF Building and Infrastructure who is both a builder and an engineer, is standing in Skedsmokorset in Akershus county, in the south-eastern part of the country. Two merry eyes peer out from underneath a fiery red helmet. Dokka’s daily work is exploring the potential in green building technologies.
In the mild autumn rain, Dokka shows off his newest babies. They are 42 years old and four storeys high. Some still look a little tired behind scaffolding and tarpaulins. Others are nearly finished with their renovation. These are the first of existing dwellings in Norway that will be converted into passive homes. This label is reserved for buildings with extremely low heat loss and low energy consumption – and that use renewable energy from local sources to provide most of their remaining energy needs.
A comprehensive renovation is about to transform these seven apartment blocks into futuristic energy efficient housing. Dokka has been an expert adviser on energy and indoor air quality issues throughout all stages of the metamorphosis, as he has been with other passive housing in a number of previous projects around the country.
“Before the craftsmen arrived, these apartments needed upwards of approximately 300 kilowatt hours per square metre per year. When the workers pack up their tools and are done, that number will have shrunk to 80,” he said.
The summer of protests
Last summer, Norwegian newspapers and television channels were full of news about protests. Plans for gigantic transmission lines and towers through Hardangervidda, a wild high mountain plateau in central Norway, had local mayors up in arms and environmental organizations rattling their sabres. Sure, people need electricity, but to sacrifice the natural environment to slow down global climate change is going too far, they argued.
In years past, the protests were about wind turbines. Who likes to look at enormous wind turbine towers through the car windscreen? Then there was Norway’s “lunar landing” – a clean burning gas-fired energy plant slated for Mongstad, in southern Norway. People weren’t protesting about the plant itself, but that the technology to make it clean was too expensive, and that it was taking too long to build.
In the thick of the protests over the Hardangervidda transmission lines, Norwegian Prime Minister Jens Stoltenberg appeared on the evening news on national television. His message was simple: he reiterated that the project was all about the energy crisis and ensuring a dependable electricity supply for Norway. He reminded his listeners that mid-Norway had had to import electricity from Sweden the previous winter. We must have this project, he stated. We must ensure that there is heat and light in thousands of homes during our cold winters.
Many bought his argument. Others refused and would not accede to the idea that we must obtain new energy sources at all costs. Because – must we?
Potential and realism
The concept of energy efficiency seems to have emerged anew in Norway over the past year. While most consumers think of energy efficiency as saving a few kilowatt hours with efficient bulbs and heat pumps, the kind of energy efficiency we’re talking about here involves public buildings and industry – and reductions that make a real difference.
“The rehabilitation of forty-year-old apartment buildings in Skedsmo so that they meet passive housing standards is a radical measure. It shows how far we’ve come in terms of energy efficiency in buildings. But if the Norwegian building stock is going to reach ambitious energy goals by 2040, we are going to have to call out the big guns,” says Inger Andresen at SINTEF.
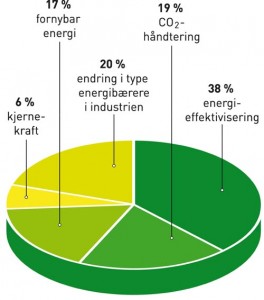
ENERGY EFFICIENCY IS MOST IMPORTANT
These are the measures needed by 2050 to reduce greenhouse gas emissions. Energy efficiency will enable us to use less energy in the form of electricity, petrol, gas and district heating.
Source: IEA
“The opportunities for savings in industry are equally large,” adds Andresen’s colleague Anne Karin Hemmingsen. As one of the leaders of the Norwegian strategic initiative called Energi21, she is behind a recent report that will have a good deal to say about how Norwegian industry will become more energy efficient in the future.
In other words, a lot is happening, and ambitions are high. But the research community has also raised some warning flags:
“If energy efficiency is going to account for nearly half of our cuts in greenhouse gas emissions, we need new knowledge and new solutions based on research. However, the national research funding that is devoted to energy efficiency accounts for only a few per cent of the total funding pool of NOK 320 million – of which renewable energy gets the lion’s share,” said Andresen.
“We need an energy revolution,” adds Hemmingsen, “and the way to get there is to conduct research in areas that the various branches of industry have in common – such as heat recovery.”
“But couldn’t the fact that scientists want more money for research be considered suspect, since it is in their own best interest?”
“True, but nevertheless, if energy efficiency is going to provide a huge cut in our energy demand, we have to have the financial and intellectual ability to make those cuts,” Hemmingsen says.
I. Streamlining manufacturing
It is an early September morning. Six women and eleven men are sitting in discussion around a conference table in the Radisson Blu Hotel near Trondheim. Ideas, experience and different viewpoints are exchanged at a rapid pace. These men and women around the table are scientists and representatives of Enova, the Research Council of Norway and energy-intensive industries such as Norske Skog, Statoil and Hydro.
Ideas about energy efficiency are foremost in their minds – these are, after all, the brains behind “Energi21”, the expert group that will prepare the country’s energy conservation strategy and provide technical support to politicians. Now they are gathered for a workshop.
The grey wall in the meeting room is covered with figures and graphs from a video projector. The numbers send a clear message: If climate targets described by the International Energy Agency are to be reached by 2050, energy efficiency must be one of the main contributors. More than 1/3 of emissions reductions will be achieved through smarter energy use. This means that industry must contribute a substantial amount. Now the expert group has to analyse the opportunities and shortcomings and come up with a short- and longterm national strategy.
SINTEF researcher Anne Karin Hemmingsen has one main message for politicians: Energy conservation is about more than just reducing greenhouse gas emissions: there is great potential for value creation in using energy more wisely. If Norwegian industry manages to reduce its energy consumption by 20 per cent by 2020, while using these savings for new industrial production, we are talking about large sums of money.
Preliminary calculations show that it is possible to save up to 20-24 TWH by using new knowledge and new approaches – in addition to existing technology.
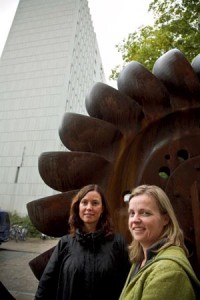
RADICAL SOLUTIONS
The opportunities for saving energy are huge in both Norwegian homes and industrial buildings, according to SINTEF researchers Anne Karin Hemmingsen and Inger Andresen. “But there need to be radical measures based on new approaches and new knowledge.”
Photo: Thor Nielsen
“This will provide billions of kroner in revenues if we use the proceeds for new production,” she says, looking out over the group.
“One of the things we need is more research on precisely this issue. That will help with policy decisions,” responds one of the participants.
“Excellent, that we can deliver! Today we have the opportunity to contribute. Prime Minister Stoltenberg has promised that if we recommend good ideas, he will provide the money. But we need concrete solutions,” says Are-Magne Kregnes from Siemens, who is leading the meeting.
Then the working groups go off to work on their own, ready to develop ideas that can be put into practice. Three hours of intense work with pen and pads of paper will result in the foundation for their strategy. The conclusions will then be sent to the Ministry of Petroleum and Energy, which will take a decision on the recommendations in the spring of 2011.
Kregnes, who has set aside time for Gemini, collects his papers and drops down into a chair.
“It’s easy to get scientists involved in new thinking. That’s their job. It is more difficult to get industry to pay the price and take concrete measures,” he notes.
“Yes, but how are you going to do it?”
“Our approach is to emphasize that industry itself must decide what is important. If they feel they have some ownership of the new ideas – it may be that they then will focus on research. In addition, the national energy policy and the framework for the future must be absolutely clear, or Norwegian industry can’t realistically set long term goals.”
“What kinds of concrete suggestions have your groups come up with?”
“There’s a lot of thinking right now about combinations, industry clusters and how to make further use of energy – such as by using waste heat from industry. Elkem Thamshavn does this today: The facility uses the heat in the exhaust gases from the power plant and produces electricity of 180 GWh, which corresponds to what 24 windmills can produce.”
The difference, however, is that while wind farms get large grants from the Norwegian government-funded organizations called Enova and Innovation Norway, Thamshavn gets less subsidies per kWh. Here we are talking about getting a change of attitude by the authorities in charge of creating financial incentives. They must be able to see that energy is not just a commodity, but an input that can create value for Norway.
Less power – more aluminium
A few hours drive southwest from Thamshavn is Hydro’s Sunndal aluminium plant – another industry giant that is working to use more of its waste heat than it does today.
Nestled between the steep mountain walls of Sunndalsøra, the company transforms huge amounts of alumina from remote corners of planet into aluminium metal, one of Norway’s main export commodities. The plant in Sunndalsøra is the largest and most modern in Europe for the primary production of aluminium.
Approximately 18.5 TWh of electricity – about every eighth kilowatt-hour of power consumed in Norway in a normal year – is used to produce this silver-grey material in this country. About half of the electricity that is consumed by the electrolysis cells is “baked into” the metal. The remaining is released as heat.
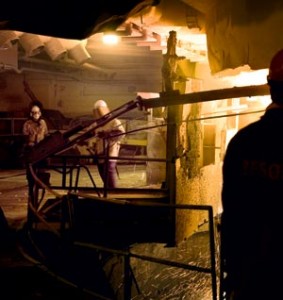
REUSING SURPLUS ENERGY
Increasing industrial energy efficiency is very much about planning industry clusters and how to use waste heat. At Elkem Thamshavn outside Orkanger, waste heat is used in this way for both heating and producing electricity.
Photo: Thor Nielsen
“The efficiency is similar to that of a modern gas-fired power plant. But the exhaust gas from a primary mill in the aluminium industry has a significantly lower temperature than the flue gas from Thamshavn and the rest of the ferrosilicon industry. Today it is not economically viable to produce electricity from our surplus heat,” says Odd-Arne Lorentsen, programme leader for Hydro Primary Metals.
He explains that Hydro’s main energy efficiency effort in the primary metal works is to reduce the amount of energy required to produce each kilogramme of aluminium.
“According to Statistics Norway, the country’s industrial electricity price has almost doubled over the last ten years. Hydro is currently making approximately 40 per cent more aluminium out of each kilowatt-hour of electricity than we did in 1960, and our ambition is to do more to strengthen our international competitiveness. But we also have various research efforts started that hopefully can make energy recycling profitable in the near future,” says Lorentsen, and lists projects that Hydro is running on its own and together with NTNU and SINTEF.
The programme manager works with technology development at Hydro’s Research Centre in Porsgrunn, but is also an adjunct professor at NTNU. He emphasizes that it is much more efficient to deliver the surplus heat to customers who can use the heat directly than to try to recycle the power.
“First we have to get enough customers for all the heat, and then we have to have a distribution infrastructure for the heat. We have district heating plants in both Høyanger and Sunndal that use the surplus heat from the plant, so we know it is possible. But the investment costs are significant and require a long-term commitment,” says Lorentsen, adding:
“Today, metals and alloys are produced in more than 20 communities throughout Norway, and all have surplus heat. In theory we could have heated all of Trondheim with the surplus heat from the Sunndal plant. But the city is not in this valley! In other words, the best way to improve Norwegian energy efficiency would have been if we could have gathered producers and consumers of energy in the same place, and then let them use the surplus energy with respect to the high and low temperatures from our plant. The addition of a dairy and some nurseries would help fuel growth in the local economy in both summer and winter.”
A pioneer cluster in Jæren
In the town of Jæren, energy pioneers have created just the kind of interdependent economy that the aluminium professor envisions.
Led by Tine, the Norwegian dairy co-operative, a handful of companies in the food industry have joined forces to build a facility that distributes surplus heat from the companies’ cooling and refrigeration plant to a heat pump. The district heating supplies heat to the businesses – plus enough to warm a greenhouse for a new nursery that was established in the neighbourhood under the apt name of the “the Environmental Nursery.” In return, the companies that supply heat to the district heating system get cold water back, which helps them reduce their energy consumption.
Senior researcher Tom Ståle Nordtvedt at SINTEF is special adviser to the project, with responsibility for managing the technological demands that will arise over time. He explains that the companies in Jæren are the first in Norway that have joined forces to swap low temperature surplus heat.
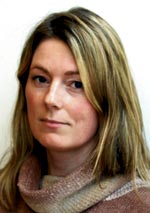
TECHNOLOGY AND ATTITUDES
Professor Marianne Ryghaug at NTNU argues that people’s attitudes are as important as technological solutions, and that there is no clear correlation between people’s environmental awareness and their energy consumption.
Photo: Tor H. Monsen/NTNU Info
“Technologically, this has been possible for a long time. But the biggest obstacle for many has been to decide who will make the investment and how benefits should be distributed. At Jæren, Tine has shown that it is possible to solve this problem,” says Nordtvedt.
The researcher has more good news.
SINTEF has recently helped a real estate developer to calculate the energy gains and CO2 cuts related to a “Jæren-type” approach for a planned industrial area in Østlandet that will be used for food distributors and commercial and service companies.
“Our analysis showed that the extra costs of heat distribution will be paid back in a couple of months. The numbers also show that this measure will shrink the energy consumption of the business cluster as a whole by 20 per cent. When these kinds of numbers are known among the country’s real estate developers, we will soon see more of these projects popping up,” predicts Nordtvedt.
II. Streamlining the building industry
In Skedsmokorset, the rain has cleared. Earlier this autumn, Tor Helge Dokka helped present the report “Energy efficiency of buildings” to the authorities.
Dokka and the other members of the expert committee have concluded that it is realistic to shrink the energy use from building use from 80 to 70 TWh (billion kilowatt hours) by 2020, and that it is possible to halve that number to 40 TWh by 2040.
Now Dokka shares with Gemini the kinds of actions that will be needed to shrink the energy consumption of the residents in the seven blocks in front of us. The list is long: Extra insulation. Triple-glazed windows to prevent “cold drafts”, and to reduce heat loss while allowing most of the Sun’s light and heat through. Super-insulated balcony doors. Products and measures to reduce air leakage to a minimum. The elimination of cold bridges. A ventilation system with highly efficient heat recovery.
The report says that the bulk of energy that will be cut by 2020 must be made in existing buildings. But not all homeowners who want to help will have to be as thorough as this housing project has been in its renovation for the goals of the report to be achieved.
“We believe half of the potential can be reached by using simple measures, such as replacement of windows, installation of heat pumps, insulation of the attic or the like. But the other half will have to come from complete rehabilitation,” says Dokka.
A three-parted mantra
Whip. Carrot. Expertise. From his office in Trondheim, Inger Andresen presents his version of what his colleague Tor Helge is talking about.
“Okay. Which mantra is this?”

FOLLOWING GOOD EXAMPLES
In the US, the Rocky Mountain Institute calculated that if the 40 least efficient states adopted the same energy efficiency measures as the 10 most efficient states have, the country’s energy consumption would reduced by one-third.
Source: Lester Brown: Plan B 4.0
“It is what is in the report that Tor Helge is referring to. There will have to be requirements for both industry and individuals via regulation. So there will have to be financial support and some guidance along the way. And we will have to have the expertise needed to change behaviour: the construction industry must be educated in everything new, and researchers need to generate new knowledge to find better solutions.”
The whip
Setting requirements for industries and construction is clearly necessary.
In a larger survey of 1800 companies in Norway, Sweden and Denmark, only 4 of 10 Norwegian companies had implemented energy-saving measures. Enova, a public enterprise owned by the Norwegian Ministry of Petroleum and Energy designed to promote energy saving measures, was virtually unknown to Norwegian business leaders. Only 36 of 600 managers responded that they knew about the funding opportunities here.
Norwegian politicians have traditionally used financial incentives combined with information to end users to create incentives to change – instead of strict requirements. “We see that it is a little different in neighbouring countries that have not been blessed with cheap hydroelectric power,” says Professor Marianne Ryghaug at NTNU, who studies environmentally friendly energy.
She believes the government should demonstrate its willingness for political action by setting requirements. “As long as climate change solutions are removed from our everyday lives, like the ‘lunar landing’ gas plant in Mongstad and climate quotas, we will not engage the population. In other words, what the politicians are doing on the energy front does not seem relevant to individuals.”
Ryghaug also believes that one of the reasons that sound energy approaches are often ignored is due to the way that the construction industry is cobbled together: it is fragmented, with many small players who are eager to build in the cheapest manner possible. It’s all about short-term profit.
… And then something happens
Now, however, the requirements are starting to come. Some have already been levelled. The Norwegian government has announced a gradual tightening of building regulations in the period from 2015-2020. From then on, all new Norwegian buildings must be passive. In 2040, energy use in buildings will be halved in relation to current levels. The average energy consumption in buildings is currently at 220 kilowatt hours per square metre – but the new technical regulations will lower that requirement to 120 kilowatt hours.
To reach the EU target that new buildings should be “almost zero energy buildings” in 2020, the expert group that Tor Helge Dokka is a part of is recommending stringent energy standards for new buildings. They believe it will help the market to mature and develop solutions. The expert group has unanimously agreed to propose requirements that new buildings be “almost zero energy” by 2020. And everyone – except the Building Industry Association (BNL) – also wants the introduction of energy standards that would require new buildings be passive by 2015.
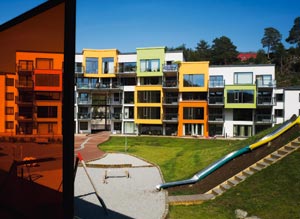
NORWAY’S MOST WELL-KNOWN
LøvÃ¥shagen condominium outside Bergen are Norway’s most famous example of low-energy homes, and are Enova’s model for how these homes should be built.
Photo: Løvåshagen
The authorities have also begun to act on the research side: last year, eight Norwegian research groups were awarded status as research centres for sustainable energy, and at NTNU/SINTEF, researchers are working on the Zero Emission Buildings/Zero Energy Houses (ZEB) project, in addition to two research projects that involve industry as partners. CREATIV is a consortium designed to develop new technologies for energy-efficient heating and cooling processes and to find ways to use waste heat from Norwegian industry, while the EFFORT project is looking at improving the energy efficiency of offshore installations. The results from these efforts will come in the years ahead.
Carrot
It is widely known that the greatest potential for energy efficiency in buildings is found in the structures that are already here. Yet there is a kind of built-in inertia on the private front. We are well aware that heat pumps are a smart investment. We also know that there are significant advantages to different construction approaches, but we don’t use them. Our neighbours need to buy the heat pump, build differently and show off their electric bill before we consider changing.
Norwegians are still using three times as much power as the Danes, and twice as much as the Swedes, and only one out of ten Norwegians has taken the trouble of switching to a cheaper electricity supplier.
“This is about facilitation, or ‘the carrot’, as I call it,” says Inger Andresen. “It has to be easy for consumers to get hold of things and learn about solutions.”
Andresen said that she is repeatedly called by private residential builders who do not have access to professional help on energy conservation.
“They ask if I know someone who can help them, or if I think that carpenters or people at the local building supply store can give them good advice. Unfortunately, the reality is that there are no professionals who can provide good, comprehensive solutions for existing homes. However, there are some who sell heat pumps, others who sell insulation, and some who sell control systems – so it becomes difficult for the homeowner to figure out what is the best option.”
“So what would be the carrot here?”
“If there were companies that homeowners could to contact that would provide the whole package – whatever was the best combination of solutions for your house, and that had carpenters and other craftsmen, delivered consulting services and brought in offers from multiple product vendors. And that there was financial support for these kinds of initiatives.”
Expertise
Making the transition from constructing ordinary homes to building super-insulated buildings where every action is done to reduce heat loss is something that is not done overnight. Low-energy, passive and zero-energy homes will change the lives of everyone involved in the construction industry. In a few years, the requirements to build passive housing will change the way we order, plan, design, construct, operate and manage structures.
The CEO of the Housing Manufacturers Association, Per Jaeger, told Byggeindustrien, a building trade magazine, that “the requirement for passive structures means that all of the players in our industry will have to adapt. The old truths will no longer apply, and we will have stop with many of the approaches and construction methods that we use today. We must not underestimate the enormous challenge that it will take to implement such a change …”
The expert committee behind the report “Energy efficiency of buildings”, says that the construction industry will need a systematic approach to continuing education. The researchers point out though that there is a big challenge in training the 200 000 to 300 000 people working in the industry to ensure that everyone has the expertise they will need to build energy-efficient structures.
Research and longterm
“Piecemeal” is a term that Inger Andresen and Anne Karin Hemmingsen constantly raise. They argue that there will be no impetus for energy efficiency if there are only short-term, makeshift solutions. Researchers must develop both existing products – while they are working with sophisticated, long-term solutions if they are to help in the speedy implementation of long-term energy-efficiency measures.
Berit Time at SINTEF supports this. She works with facades in the ZEB (Zero Emission Buildings) research group. She cites as an example the passive houses that are now coming fully into new development projects. A passive house built with traditional insulation materials will have walls of 20-25 cm thickness to provide good insulation. But zero-energy houses will require wall thicknesses of 40-45 cm.
“That will reduce the floor area, and will create challenges related to daylight. We need more effective insulation materials that provide thinner walls. Especially in urban, dense residential areas, this is important.”
“What’s new?”
“Now we are talking about multi-functional facades, which are facades that meet the basic needs for insulation, but that also have elements in them to produce energy for the building. We are working with other partners in Europe, where solar cells and solar collectors are more common. But we have to look at how other products and approaches can be used in our climate and in Norwegian architecture.”
“Can you provide some examples?”
“We have tested a vacuum insulation panel that insulates five to ten times better than mineral wool. The panels consist of a porous silicon core – surrounded by a dense film – are sealed while there is almost a vacuum in the core material. In this way, 40 cm of mineral wool can be replaced by a 4 cm panel.”
“But …? There always tends to be a but.”
“The insulating value of the panel tends to degrade over time and is not very robust. If it is punctured, it loses its vacuum. A European manufacturer has used the panel along with traditional insulation, and we will now try that approach in Norwegian conditions.”
A few doors down the hallway is Time’s colleague, Bjørn Petter Jelle. He is working with smart windows that can block out or let in desirable amounts of solar energy. The window is constructed of glass that has thin coatings that can change from transparent to other colours. Wolfram oxide is one widely used material.
Jelle said that the principle behind smart windows is to let in maximum sunlight and radiation – especially in winter, so you can use less energy for heating. Shutting out sunlight may also be a plus for large office buildings, so they can thus avoid the use of energy for cooling.
“Here in Trondheim we will now go ahead and create our own materials to test. For example, we will study whether it is possible to combine different materials in a sandwich. In addition, we will test existing smart windows that are on sale to see how well they are adapted to Norwegian conditions.”
Solar hot water heating
The afternoon light has gone from the seven blocks of flats at Skedsmokorset. But on one of the roofs Gemini sees some kind of wacky structure and piping.
“Those are super-efficient solar collectors with a large pump to supply water tanks and heating systems throughout the housing with green heat,” says Tor Helge Dokka, SINTEF.
Large numbers of young people rush past us on the way home from school. But few of them turn into the apartment blocks. We are told that 96 per cent of the residents here are between 55 and 70 years old.
“People have at times had to do without water in their bathrooms and kitchens during the renovation. Have there been complaints that it is just too disruptive when these old housing blocks are transformed into passive housing?”
“No, actually not,” Dokka says. “The concerns have been more about things like a few paint spots here and there. And that wallpaper from 1968 can’t be found in stores anymore!”
But even if the old wallpaper has to be removed, the residents benefit from getting rid of cold floors and heat loss from the windows, says Dokka.
“Passive construction increases comfort for the occupants while shrinking fuel costs. And it is good for the environment. A win-win situation, if you ask me!”
By Svein Tønseth, Christina Benjaminsen and Åse Dragland.