Construction solution extracts heat directly from the earth
Using a completely new piling joint, geothermal heat can be extracted directly via the piles used to anchor buildings in the ground. The invention makes it easier, quicker, cheaper and safer to use environmentally friendly energy.
The new piling joint, which has now been patented by NTNU Technology Transfer AS, connects pre-fabricated concrete elements to achieve the desired length in a quick and safe manner. The piles are anchored in bedrock and equipped to use geothermal heat directly to heat or cool buildings.
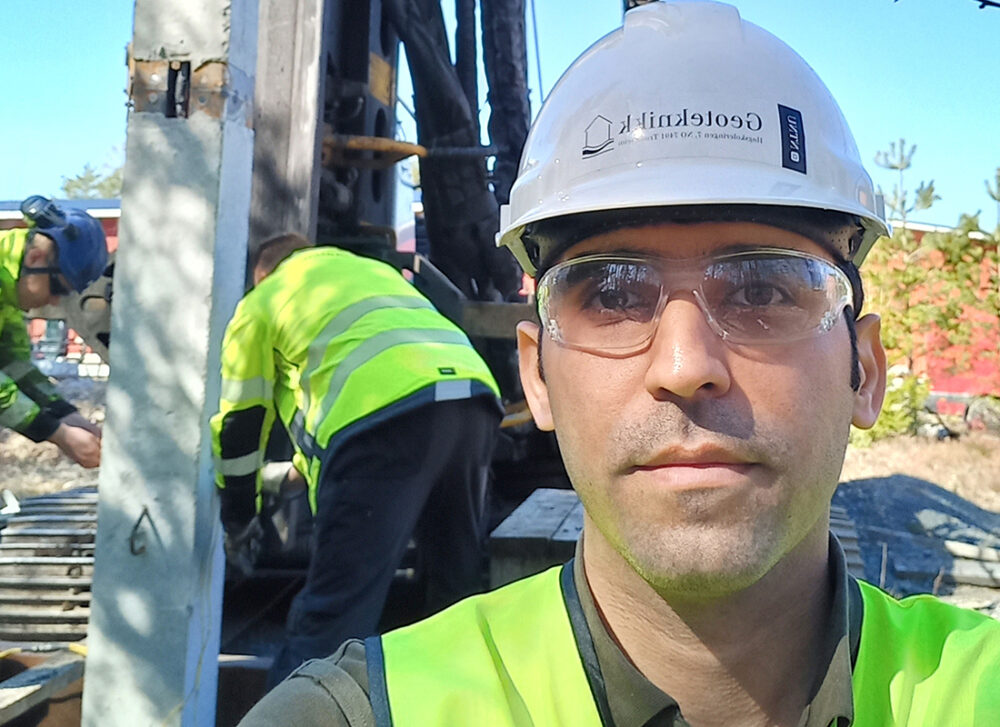
The key to the DEP Joint (Driven Energy Piles) project is the steel pile joint that can be seen at the top of the pile in the background. The joint has been further developed by PhD candidate Habibollah Sadeghi from the Department of Civil and Environmental Engineering at NTNU.
No need to bore separate wells
The new solution means that building owners who want to use geothermal heat no longer need to bore separate wells to obtain it, a process that is both costly and challenging.
So far, no-one has been able to extract geothermal heat directly through the foundations of a building in an affordable and efficient manner.
Connections using the LEGO principle
The key to the DEP Joint (Driven Energy Piles) project is a square pile joint made from steel, which has been further developed by PhD candidate Habibollah Sadeghi at the Department of Civil and Environmental Engineering at NTNU.
The joint piece is equipped with two male connectors and two female connectors that can be quickly and easily connected to one another. Two steel bolts are used to lock the joints together.
“It’s reminiscent of the way you build LEGO,” says Sadeghi, who designed some new openings on the sides of the pile joints.
The openings allow for embedded tubes to be connected safely and efficiently without affecting the load-bearing capacity of the piles.
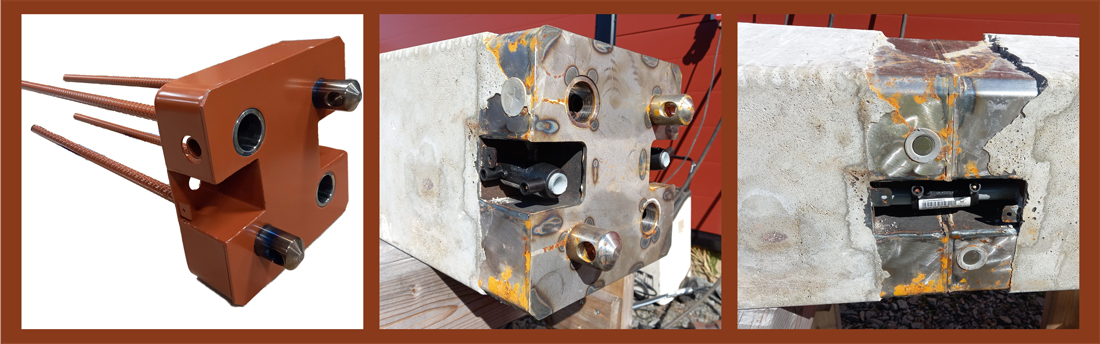
The key to the DEP Joint project is the square steel joint. Welded reinforcements ensure that the joint piece and the concrete element are securely attached. The steel joint is equipped with two male connections and two female connections that can be quickly and easily connected to one another and locked using a couple of steel pins. Photos: DEP Joint/Montage: Sølvi W. Normannsen
Heat with tremendous potential
After solar energy, geothermal heat is the largest available source of renewable energy. As much as 99 per cent of the earth has a temperature above 1000 degrees Celsius. Combined with heat pumps, underground structures can utilise the stable heat that is available almost right below our feet, even somewhere cold like Norway.
The technology offers many possibilities and many people are working to develop the technology so it is sufficiently efficient and safe.
First PhD in energy piles in Norway
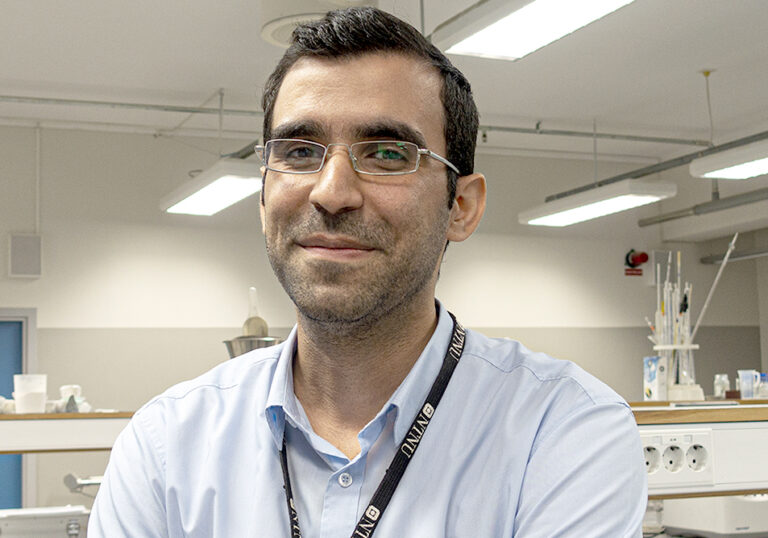
PhD candidate Habibollah Sadeghi at the Department of Civil and Environmental Engineering, NTNU. Photo: Sølvi W. Normannsen
Habibollah Sadeghi is the first person in Norway to earn a doctorate in energy piles. At the start of his studies, he consumed all the literature he was able to come across in the field.
He says that he soon realised the limitations and challenges associated with pre-cast piles. Only simple elements with relatively short lengths were available on the market. There were also no solutions available to join the concrete pile elements together.
Idea from U-Bahn in Austria
Sadeghi got the idea for a solution from a course in Switzerland and an example from Austria. There are more than 100 kilometres of recuperator tubes running through the walls, bushings and cast concrete slabs on the underground line in Jenbach.
Each year, the project harvests 175 and 437 MWh for heating and cooling respectively from the surrounding earth around tunnels and underground stations.
“The system gave me the idea of linking the pile elements together in an equally efficient and safe manner,” the PhD candidate says.
Steel to strengthen load-bearing capacity
The joint piece and the concrete element are fastened by welding steel reinforcements to the joint piece. The piles are cast at the factory and super-strong tubes, or energy loops, are cast in. These are then linked at the same as the piles when they are driven into the ground. The liquid, which is heated by geothermal heat, circulates through the loops.
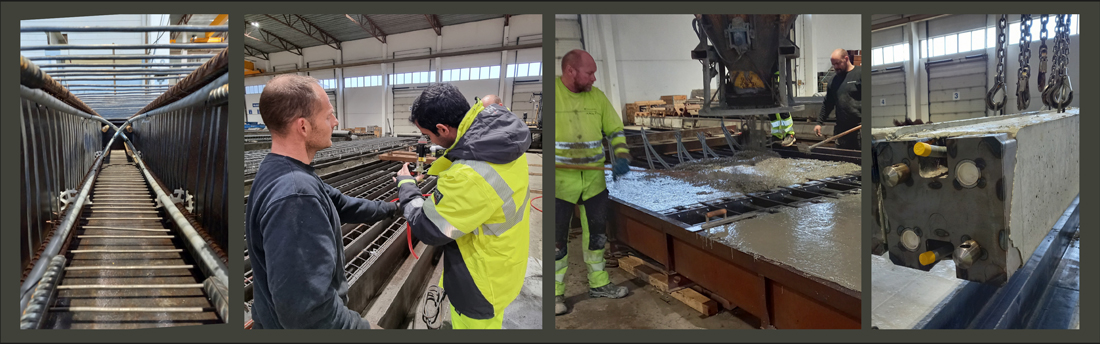
Concrete piles being cast at Sandnes & Jærbetong AS. The piles are cast in horizontal formwork and reinforced using an internal “steel corset”. This strengthens the load-bearing capacity and provides protection against shocks, vibrations and other impacts that often occur when piles are driven into the ground. Photos: DEP Joint/Montage: Sølvi W. Normannsen
Strict quality requirements
One crucial advantage of DEP Joint is that the system is based on pre-fabricated concrete piles. The piles are produced in large quantities and are therefore subject to strict quality and safety requirements.
Another advantage is that it will be much easier to check the quality of something that arrives straight from the factory than to inspect piles that have been cast in holes on site.
Sadeghi and his academic supervisor, Professor Rao Martand Singh, have worked closely with NTNU Technology Transfer AS to further develop the concept.
“There are no similar solutions available on the market today,” says Lodve Berre, a business developer at NTNU TTO.
The challenges of current wells
The wells that are bored to extract geothermal heating for newbuilds today are often 150-300 metres deep. The boreholes result in large quantities of excess soil that needs to be removed.
Ground conditions can also pose various challenges. The soil, for example, might be contaminated and require special treatment. Changes to water levels can also lead to unstable ground conditions, as well as settlement and subsidence damage.
“DEP Joint piles can be easily used without any issue in areas with contaminated soil and low water levels,” Berre explains.
More piles instead of deep holes
Since the elements need to be transported from the factory to the construction site, they cannot be longer than 12-15 metres. This is a disadvantage, as long energy loops are desirable because they can extract more heat.
DEP Joint solves this dilemma as follows:
“Instead of boring a 300-metre deep hole, we can install 12 energy piles down to the bedrock situated at a depth of 50-60 metres instead. This will allow us to extract almost the same amount of energy,” Sadeghi says.
Additional costs quickly recouped
The energy piles are slightly more expensive and take a little longer to install, but this is recouped in less than a year, according to the researcher.
In Norway, 250,000 metres of concrete piles are driven into the ground each year. Virtually all large buildings are equipped with such foundations. This, combined with the fact that the world has never before had a greater need for clean and efficient energy, lies at the heart of DEP Joint’s business concept.
“If we can reduce the energy requirements for heating and cooling of newbuilds by two thirds, it would correspond to enormous amounts of power saved globally. It would also help with the load in the power grid,” says NTNU TTO’s Berre said.
Particularly effective in cold climates
Habibollah Sadeghi has published several studies in which he has compared performance, potential and economics for various heat pump systems used in Norway and Europe.
There are many solutions available, but systems that use geothermal heat came out extremely well. The installation costs are high but are quickly recouped in relation to the service life of the building.
“In colder climates such as Norway, geothermal pumps are particularly efficient, as the temperature in the ground remains stable,” the researcher says.
Patented and ready for license agreement
DEP Joint is a FORNY (“Renew”) project funded by the Research Council of Norway, which has allocated NOK 5 million to the project.
As the employer, NTNU owns the rights to PhD candidate Sadeghi’s invention, while NTNU Technology Transfer manages the intellectual property on behalf of the University.
The company has applied for patent protection and is working to get the steel joint out into the market through licensing agreements with one or more manufacturers.
Tough tests in Finland
The initial prototypes were produced by the Finnish manufacturer Leimet Oy towards the end of 2022. Another partner, Sandnes & Jærbetong, have cast the connection in the piles.
In May 2023, the piles underwent very tough European standard impact, pressure and leakage tests at Leimet Oy. They were subsequently shipped to the University of Tampere for deflection testing.
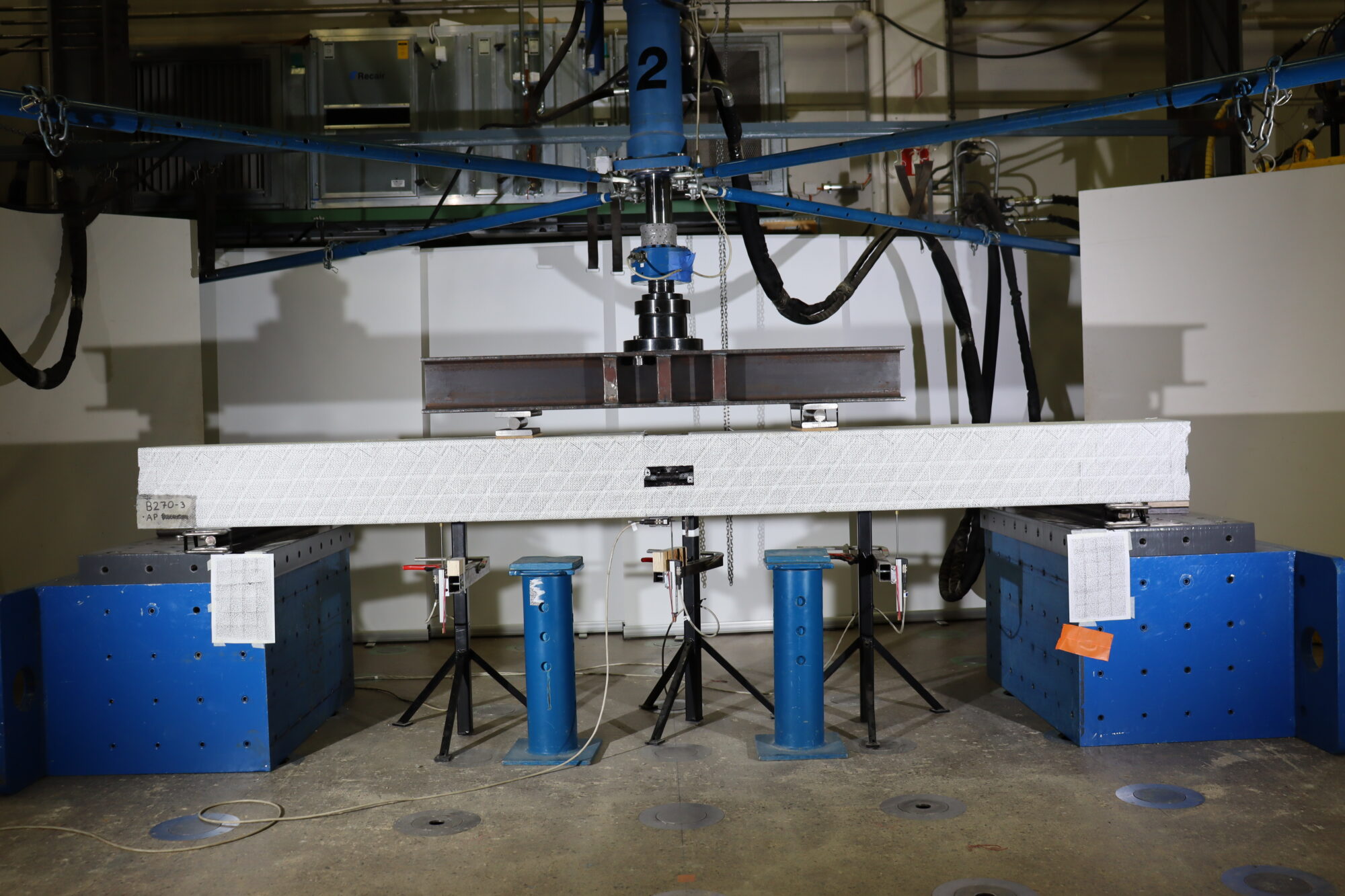
Concrete pile with steel joint undergoing deflection testing at the University of Tampere, Finland. Photo: Habibollah Sadeghi
The piles are safe, strong and impervious
The tests showed that the joints escaped unharmed and that both tubes and connections are impervious. They also found that the piles have just as good load-bearing capacity and strength as traditional, pre-cast concrete piles available on the market.
This means that DEP Joint satisfies the requirements for CE marking. It also means that the basic safety requirements have been met and that the pile joint is ready for use in the construction industry.
Global market
The potential of the project is formidable according to the project stakeholders, considering that all large buildings require foundations.
“There is a global market, as the solution is just as good for cooling as it is for heating,” says Lodve Berre from NTNU Technology Transfer.
A new energy pile will be cast in Stavanger this summer. It will be 24 metres long and will consist of a connection and two concrete elements. The pile will eventually be installed near NTNU in Trondheim, where researchers will measure how much energy it is capable of retrieving. According to Habibollah Sadeghi, another goal is to install the piles under an ordinary newbuild.
The plan is to do this in collaboration with a client, hopefully with pilot funding from ENOVA.
References:
Habibollah Sadeghi, Rao Martand Singh. Driven precast concrete geothermal energy piles: Current state of knowledge Building and Environment,
Volume 228,2023
Habibollah Sadeghi, Amir Ijaz, Rao Martand Singh. Current status of heat pumps in Norway and analysis of their performance and payback time. Sustainable Energy Technologies and Assessments, Vol. 54, 2022